LED 101 for Industrial Buildings
LED 101 for Industrial Buildings
LED 101 for Industrial Buildings
MODERN LIGHTING & ADVANCED CONTROLS
LED lighting and advanced controls have been proven to bring a range of benefits to many types of environments. This reference guide discusses the basics of LED and lighting controls technology and how it can be applied to your industrial space.
Untapped Potential
LED products are making steady inroads in replacing traditional light sources, yet most of their energy- and money-saving potential remains untapped, according to the latest update of the U.S. Department of Energy’s (DOE) report, Adoption of Light- Emitting Diodes in Common Lighting Applications.
The report goes on to note the greatest possible benefit from LED lighting will depend on connected controls that respond dynamically to changing conditions and demands. In fact, the savings achieved by connected lighting systems with advanced controls can be quite significant according to the DOE, especially for industrial applications using low and high bay LED fixtures.
Every day, building owners are discovering the incredible advantages of LED technology. From exceptional light quality and unrivaled product life span to easy controllability, LEDs have a lot to offer, including exciting Industrial Internet of Things (IIoT)-enabled outcomes.
Future-Proof
LED light fixtures present a unique opportunity because they permeate plants and warehouses like few other assets can; they are virtually everywhere from the front door to the loading dock. Additionally, they have their own power source, they can be controlled remotely, and they can be equipped with sensors capable of ingesting a variety of information. This means industrial facilities can create digital ceilings that open the door to endless smart factory outcomes leveraging the IIoT.
Consider These Savings
In its recent report, the DOE forecasts that LEDs will represent 86% of all lighting sales by 2035, and that among all types of LED lighting, low/ high bay fixtures operating in the commercial and industrial sectors have the greatest energy savings potential behind only linear fixtures. The report further notes that when connected controls are included, this savings potential increases dramatically.
GE Current, a Daintree company, has documented lighting energy savings up to 50% in plants and warehouses that have switched to LED, and up to 20% additional savings where connected controls are used, proving that with the right combination of products and solutions, facility owners can reduce their lighting energy as much as 70%.
LED Advantages
LEDs are widely considered the biggest breakthrough in lighting technology since the incandescent bulb, with the boundaries of efficacy and life having been greatly extended thanks to constant innovation.
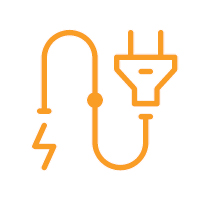
Superior Energy Efficiency
Typically, LEDs consume about 50% less electricity than traditional light sources, making substantial energy savings the most attractive feature to many industrial facility owners. A standard T8 fluorescent lamp, for instance, uses roughly 250 watts, whereas an equivalent LED solution may use just 130 watts. Multiplied across hundreds or thousands of fixtures in a factory or warehouse, these savings can be quite significant.
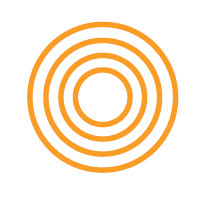
Improved Light Levels
LED fixtures can aim light hemispherically (that is, in specific directions) unlike conventional lamps and luminaires that emit light spherically in all directions. In manufacturing environments, this can suit many purposes, from directing light to specific work stations and down aisleways to illuminating rows of pallet racks for easy visibility. Most LED products offer a variety of photometric options—or light distribution patterns—to meet different requirements.
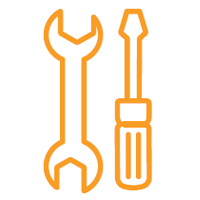
Longer Life, Less Maintenance
Unlike conventional lamps, LEDs do not “burn out”—instead they slowly dim or deteriorate over a long period of time. For example, a luminaire rated for L70 at 100,000 hours means that it is rated to depreciate to 70% of initial output after 100,000 hours of burn time. A much longer life means a significant reduction in routine maintenance needs. Especially in industrial facilities where ceiling heights can reach 60+ feet or anywhere extra precautions—and costs— come with routine relamping, LEDs can greatly reduce maintenance spending and allow you to avoid costly disruption to production.
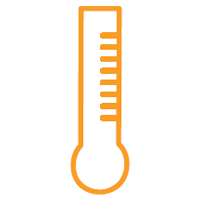
Minimal Heat Output
LEDs produce little heat, most of which is absorbed by a heat sink. Compared to fluorescent, metal halide and high-pressure sodium (HPS) lamps, LED solutions are a much cooler option for industrial environments where ambient temperature control is critical due to sensitive chemicals or processes. Less heat contribution also means HVAC systems do not have to work as hard to maintain a comfortable temperature.
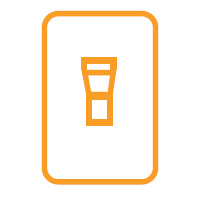
Instant-On Ability
Many fluorescent and HID lamps don’t provide full brightness immediately, often requiring about three minutes to reach maximum output. LED systems, by contrast, emit 100% brightness instantly, with no re-strike delay. For industrial facilities, this is critical in the event of a power outage or in the early morning hours during shift startup.
We asked our operators where they thought the light wasn’t bright enough to do their work, and we analyzed our lighting spend in detail to understand how LED could impact our electricity bills. It’s easy to overlook lighting until you really examine the potential that exists for a plant this size.
Industrial Facility Manager
Advanced Lighting Controls
While lighting controls can save money by keeping energy use to a minimum, few industrial facilities utilize controls or take full advantage of the system that is in place.
The good news is that a new generation of controls is making it much simpler to manage the lighting needs of large buildings. Today’s sophisticated yet easy-to-use systems can provide automated, single- or multiple-fixture control in a factory or across many sites simultaneously, enabling completely new energy-saving strategies. In fact, connected lighting sensors and controls can save facilities up to 20% more energy on top of the savings already created by LEDs.
Depending on the Goals and Vision for Your Facility, There are Three Levels of Lighting Controls to Consider:
- Standard controls for simple on/off switching, dimming and occupancy sensing (switching lights off when a space is vacant);
- Advanced controls for added capabilities like daylight harvesting (reducing light levels based on daylight conditions), smart scheduling (tailoring light output to match the operating rhythm of the facility) and task-tuning (adjusting the output of a single fixture or group of fixtures depending on the specific light level requirements of each area); and
- Connected controls that leverage lighting (with sensors embedded in the fixture) as a communications network to deliver business value that goes beyond energy management benefits. Connected lighting systems form a wireless web (sometimes referred to as a mesh network) throughout a facility that can be used to capture data and share information between devices.
A connected lighting network, as a platform for exciting IoT applications, can support everything from asset tracking to equipment maintenance, and beyond to environmental monitoring. Furthermore, you can centralize multiple sites on a single platform, allowing for even greater control and visibility across a portfolio of sites. This network can also integrate with a Building Management System (BMS) to extend to other forms of controls, unlocking even more powerful energy-management approaches.
The bottom line for building owners is that the right system can deliver big energy savings and exclusive operational benefits. As many plant operators are learning, now is the time to have a new conversation about lighting controls.
Daintree Wireless Controls solution is simple, scalable and flexible and includes advanced lighting controls, edge hardware devices and an intuitive web-based software application (DCS).
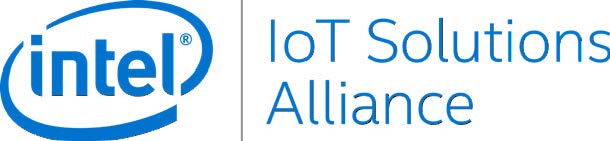
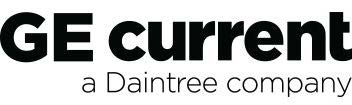
The Power of an Open Architecture
Both open-on-the-top and open-on-the-bottom, our digital solutions can easily be integrated with other third-party solutions to create a connected ecosystem that allows our clients to maximize the value of their systems.
Current, with Intel® technology, is transforming smart building management through an open, wireless control solution that maximizes the value of building assets, unlocks operational efficiencies and digitizes intelligent environments. Current is proud to be part of the Intel Internet of Things (IoT) Solutions Alliance, which includes 400+ global member companies committed to accelerating the deployment of intelligent devices and end-to-end analytics.
Learn more about the open, autonomous, ever-evolving intelligent factory and discover Current’s own network of IoT solutions providers that are connecting data from device to cloud to digital outcomes.
Intel and the Intel logo are trademarks of Intel Corporation in the U.S. and/or other countries.
LEDs in Action
Whether it’s a full-scale lighting upgrade across a large auto plant or using an advanced controls system in a small warehouse, your facility can also reap the benefits of an LED installation.
Monumental Savings at Iron Mountain
Iron Mountain’s global network of records warehouses and data repositories—over 85 million sq. ft. of space—makes lighting a crucial cost of doing business. At several of its facilities, Iron Mountain replaced old 40- and 50-watt fluorescent lamps with a 12-watt LED Refit™ Solution from Current, saving 70% in energy costs. Current also installed occupancy sensors that automatically switch lights off after five minutes when no motion is detected, creating additional savings that add up quickly.
General Motors Cuts Energy Use Across 32 Sites
General Motors recently installed 45,000 low and high bay LED fixtures with motion sensors from Current at 32 sites around the world, saving millions of dollars in annual energy expenses. For GM, lighting is a key component to driving culture change regarding energy conservation because it is the first thing employees notice when they enter a plant.
Cummins Drives Heavy-Duty ROI
Like many factories, Cummins’ Jamestown Engine Plant (JEP) used standard T8 fluorescent lights that lasted just 20,000 hours on average. With 2,800 fixtures spread across the facility, frequent changeouts were a constant frustration. Now, Albeo® ABV3 LED high bay luminaires from Current use 50% less energy, last five times longer and can be controlled individually or in zones with a wireless Daintree® system. In its first year as an LED facility, JEP saved $409,000 in energy costs .
The Right Light for Bobcat*
For Bobcat Company at its Wahpeton, North Dakota, manufacturing plant, the right light for welding, testing and assembly is essential. The facility houses 98,000 sq. ft. of production space brightly lit by Current’s Albeo® LED high bay fixtures, which reduced electricity costs by $50,000 a year. Bobcat noted its old metal halide lamps wasted light and illuminated the ceiling more than was necessary. Now, Current’s LEDs direct light only where it’s needed, helping employees focus on the task at hand.
Average Payback Period
While every facility is different, the typical plant, factory, warehouse or storage center outfitted with conventional lighting can expect a full return on investment from a complete LED retrofit within one to three years on average, based on the energy savings created.
LED Basics
An LED, or light-emitting diode, is a semiconductor that emits visible light when energized. This requires a driver, or power supply, that creates electrical pressure (voltage), pushing charge carriers through the LED. LEDs are also referred to as solid state lighting (SSL) devices. Unlike conventional incandescent and fluorescent lamps, LEDs do not use electrical filaments, plasmas or gases to create light.
“Brightness,” or light output, is quantified in lumens. Lumens provide an accurate measure of the extent to which a light source will illuminate a space or object. Watts, on the other hand, measure the rate at which energy is emitted (power).
Components and Construction
Chip and Module
Made up of multiple thin layers of semiconductor material that produce light when electrons move between the layers (known as electroluminescence); for manufacturers, achieving the desired light output, color temperature and product life span requires precise engineering to ensure just the right amount of electricity is delivered to the chip. Multiple chips are housed within a module.
Driver
Regulates power to the module and protects chips from current fluctuations (much like ballasts for fluorescent lamps).
Housing
Durable outer shell that protects and positions the light source; sound mechanical engineering prevents corrosion and humidity from degrading electrical components.
Lens
Directs light where it is needed (typically allows more control than a reflector) to minimize wasted light and needless energy consumption; different designs are used to create different effects and light distribution patterns.
LEDs from Current are:
LED Lighting Applications
LED lighting can improve visibility and efficiency in a wide variety of industrial applications, including indoor, outdoor, hazardous and NSF rated locations.
INDOOR
In industrial settings such as manufacturing plants and warehouses, lighting must be energy efficient, promote the safety and productivity of workers, be easy to maintain, and comply with a variety of building codes depending on the environment.
OUTDOOR
Outdoor commercial luminaires including area lighting, flood lighting, and roadway lighting can help facilities mitigate risk in places such as loading docks, parking garages and industrial parking lots.
HAZARDOUS LOCATIONS
In many hazardous environments where lights rated for Class 1, Division 2, Groups A, B, C & D fixtures are required, such as oil refineries, petrochemical plants, and nuclear power plants, Current’s LED Hazardous Location Lamps can be used. Current hazardous location lighting can be used for a variety of environments and applications including new construction, locations with high ambient temperatures, wet rated locations, and areas where explosive vapors and/or fumes are present.
NSF RATED APPLICATIONS
For applications such as food processing, food production and cold storage, LED fixtures with NSF and IP ratings may be required to meet the demands of these environments. NSF rated lighting is ideal for areas that may include wet and/or corrosive environments where sealed fixtures are required due to the levels of splash zone.
Options for Industrial Facilities
No matter your lighting need, it can be addressed by LEDs. Common product types in plants, warehouses and storage centers include:
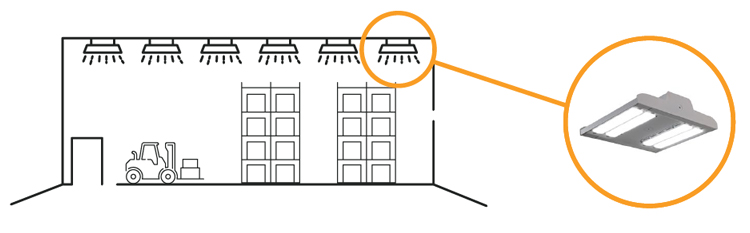
HIGH BAY FIXTURES
Designed for mounting heights of 20 feet (6 meters) or more, these can provide specific light patterns to the floor for optimal visibility and safety.
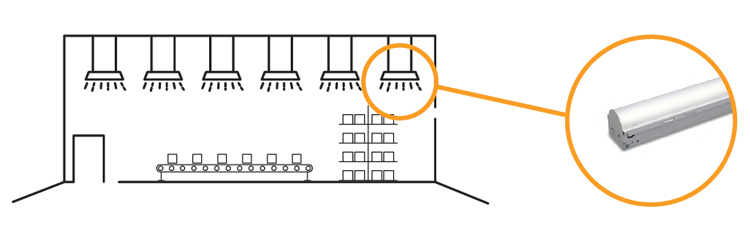
LOW BAY FIXTURES
Designed for mounting heights of 20 feet (6 meters) or less, including task lighting for assembly lines, manufacturing areas and individual work stations.
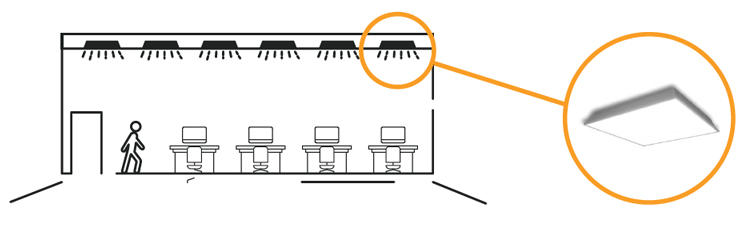
RECESSED INDOOR LIGHTING
that can replace outdated fluorescent lamps and tubes in drop ceilings in offices and other commercial spaces.
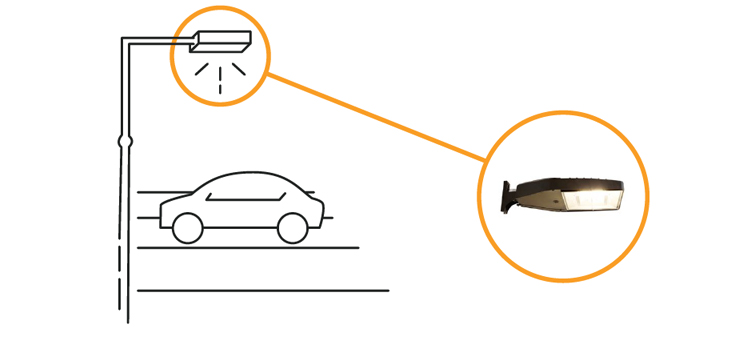
AREA LIGHTING
Brightly illuminates parking lots and pathways while saving significantly more energy than standard high-intensity discharge (HID) systems.
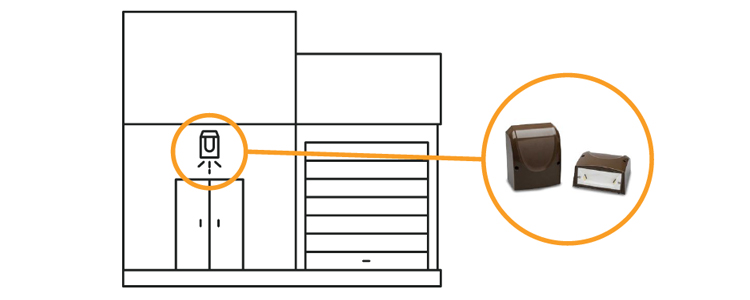
WALL-MOUNTED LUMINAIRES
Provide effective security light levels for building exteriors.
Lighting the Way Forward
Factories around the world are getting smarter and turning to new digital technologies to improve how they conduct business. As manufacturers across all regions realize that intelligent environments are the future, they also recognize the need for a better infrastructure that can support the Industrial Internet of Things (IoT).
IoT within an industrial space is a critical step to building a truly smart facility. Technologies such as robotics, augmented and virtual realities, machine-to-machine communication, connected logistics, predictive maintenance and more are becoming ubiquitous and will shape the future of manufacturing. The tools of tomorrow can help optimize performance, improve decision-making and make organizations more competitive in an increasingly global marketplace. For those who want to stay ahead of the curve, embracing Industry 4.0 is the only way to do it.
Investing in IoT technologies is tricky, however: Technology changes at such a rapid pace, many organizations are not sure where to begin or how to ensure that budget isn’t wasted on soon-to-be-obsolete strategies. That’s why lighting is the perfect place to start.
Because most light fixtures are found in ceilings or are suspended overhead, it gives them a unique bird’s-eye vantage point. By adding sensors and advanced controls to lights, building owners can begin to leverage this vantage point to create innovative and compelling use cases.
For example, a connected ceiling can enable real-time location-based systems for asset tracking. Bluetooth Low-Energy (BLE) or radio frequency identification (RFID) sensors in the fixture can read BLE or RFID tags on assets and determine their position and movement. This can be used to track vehicles, equipment, goods and even people moving throughout the facility.
When Edison invented electric light, his challenge didn’t end there—he next had to figure out how to scale and optimize his creation. Well over a century later, Current is revisiting this challenge with LEDs. Tapping into the full power of LED technology while embracing Industry 4.0 allows Current to explore how the industrial sector not only can adapt, but thrive in this changing world.
Interested in Learning More?
By assessing your facility’s lighting, you can determine if an LED solution with advanced controls is right for you—and that starts with a lighting audit conducted by a trusted partner.
Contact GE Current, a Daintree company, to explore the best options for your industrial building.