Automotive Digitization: Time to Shift Focus to Intelligent Environments
Automotive Digitization: Time to Shift Focus to Intelligent Environments
Authored by Frost & Sullivan
INTRODUCTION TO THE INDUSTRIAL INTERNET OF THINGS (IOT)
We are in the midst of the fourth industrial revolution known as Industry 4.0. Enabled by the Industrial Internet of Things (IIoT) and driven by smart factories, industries are embracing new technology to boost production capabilities and realize massive cost savings. Frost & Sullivan projects the financial implications of smart factories at $150 billion for automotive manufacturers in just three to five years. Realizing the power of leveraging new advancements, namely in industrial LED and sensor technology, manufacturers have started to transform their automated, standalone factories into fully connected, flexible spaces.
Smart factories are the culmination of many disruptive technologies such as wireless sensor networks, machine‑to-machine connectivity, IP-based communication, predictive maintenance, connected logistics, additive manufacturing, industrial robotics, smart energy management, digital ceilings, and drones. These advancements support process improvements, reduce energy consumption, provide the ability to refine product costs, and lead to faster time-to-market. Integrating these new technologies transforms the factory into an intelligent environment. Smart factories provide management with the information and tools to properly measure performance, prioritize how they compete, and guide investment decisions.
Exhibit 1: Key Technologies and Components of a Digital Factory, Global, 2018
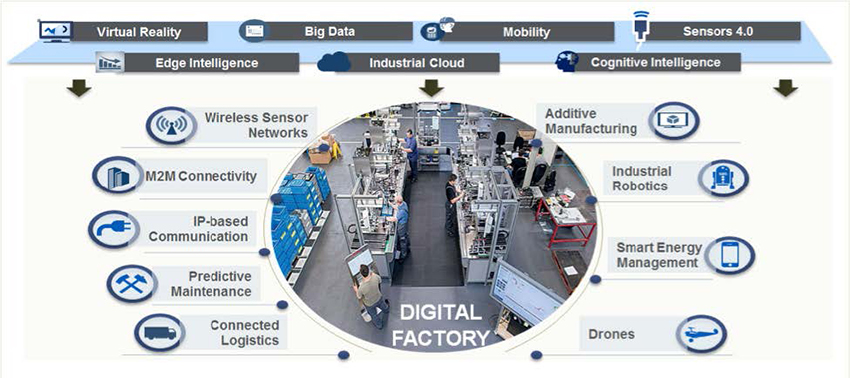
Machine-to-machine communication in a centralized system makes this ecosystem function. Production processes become more efficient by integrating data from system-wide physical, operational, and human assets. Real-time data monitoring allows plant operators to be more proactive with predictive maintenance, which can reduce costs and prevent unforeseen shutdowns. That’s particularly important because plant shutdowns cause automotive manufacturers to endure major financial setbacks at an estimated rate of $20,000 per minute (Source: HP 2018). Inventory tracking systems and energy management systems are more efficient than ever. Data generation and usage ultimately determine a manufacturer’s maturity, setting it apart from competitors.
Smart factories augment labor productivity, process efficiency, and task prioritization to yield cost savings. Intelligent automation processes shift responsibility from human to machine, minimizing response time and the possibility for human error. Quality management, task optimization, and labor productivity increase dramatically as more processes become automated. The implications mean that roles in the workplace are changing, with some estimates projecting that 9% of jobs are currently automatable in OECD countries (Source: OECD 2016). The digitization of operations across the entire manufacturing network helps humans make better, more informed decisions. Auto manufacturers already utilize this tech in smart factories across the globe, creating intelligent environments to solve production and energy needs.
SHIFT TO INTELLIGENT ENVIRONMENTS
The automotive industry was an early adopter of intelligent environments, investing anywhere from $4 billion to $5 billion on smart infrastructure in the past five years. While OEMs in Europe have been the fastest to embrace the IIoT, North America is catching up rapidly. Frost & Sullivan research indicates that Audi, BMW, and General Motors have invested heavily in IIoT within their plants in the US and Mexico. Audi’s factory in San Jose, Mexico, focuses on centralized production control, RFID, smart logistics, and electronic quality processes to vastly improve inventory management and inbound logistics. BMW’s plant in Spartanburg, South Carolina, focuses on collaborative robots for more efficient production processes. General Motors is retrofitting its plants with more energy-efficient LED lighting and incorporating sensors and controls to create smart objects and reduce overall energy consumption.
Exhibit 2: Automaker Strategies on Intelligent Environments, US, 2018
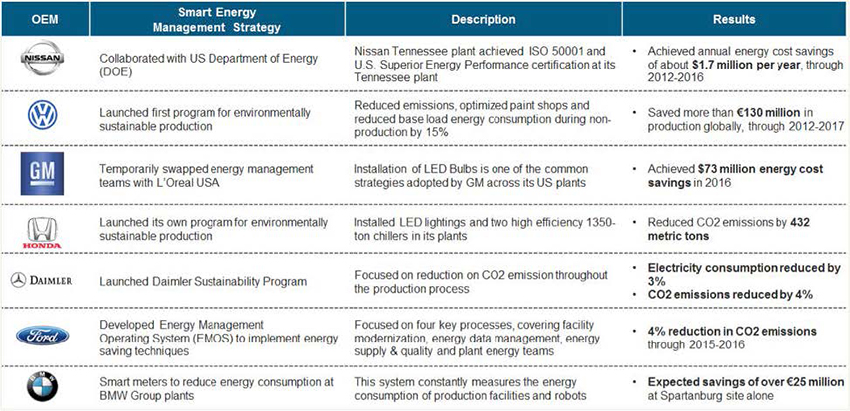
Intelligent environments help automotive manufacturers realize massive energy consumption reductions. GM is committed to reducing energy intensity by 20% by 2020 using a 2010 baseline. To date, the company has reduced its energy by 14% by utilizing LED lighting and GE software solutions to improve inline scheduling and production monitoring, as well as data collection for existing energy systems. Smart meters help identify excess energy consumption, providing actionable data to reduce usage. Collecting data from smart infrastructure provides the means for advanced analytics, further driving optimization, improved product quality, and reliability in production.
To comply with increasingly strict emission and energy regulations, automakers in the US are seeking expertise from outside their industry to create sustainable, intelligent environments. Manufacturers are collaborating with governments, energy companies, and startups that can help them maintain internal sustainability programs. GM has temporarily swapped energy management teams with L’Oréal USA. And by collaborating with Current, to install industrial LED bulbs across all US plants, GM achieved a massive energy cost savings of $73 million in 2016.
Meanwhile, Ford has developed an energy management operating system (EMOS) to implement energy‑saving techniques. Focusing on facility modernization, energy data management, energy supply, and quality plant energy teams, Ford has effectively reduced CO2 emissions by 4% between 2015 and 2016. While the objectives may be different, smart factories provide an increasing number of solutions for multifaceted problems.
CURRENT—LEADING THE INTELLIGENT ENVIRONMENT MOVEMENT
IIoT vendors provide clients with smart infrastructure to achieve not only energy conservation goals, but also quality management, security, and more. Select players provide offerings such as connected factory and machine solutions for building a digital supply chain. Others focus on intelligent asset management, cognitive processes, and smart resource optimization to compose intelligent environments that make human processes more ergonomic with seamless digitization. Vendors are sculpting an ecosystem of services that harness innovations in automation, data collection, and machine connectivity to help clients reach new levels of productivity and employee satisfaction.
“The better CRI from the LED fixture has improved our employee satisfaction with their workplace. This was noticed through direct feedback from our customers,” said Breitner Marczewski, an Energy Engineer at General Motors. “Other benefits are the standardization of the products, which helps [with] procuring materials. Maintenance costs are being realized as the LED last longer, and associated with that comes improvement on safety, as you don’t need to send a maintenance crew on a lift to replace a bulb or a faulty ballast, reducing the risks of an accident—and that, for GM, is paramount as we are committed to safety in everything we do.”
Current, assists manufacturers in transforming standalone, analog spaces into more automated, intelligent environments. Current drives value with features ranging from lighting controls to data-capturing sensors to more sophisticated software applications. Offerings such as LED sensors, analytics platforms, and third-party applications augment production, maintenance, and inventory processes to elevate the performance of the building, staff, and equipment. The Current intelligent infrastructure is “open-at-the-top” and “open-at-the-bottom,” allowing users to easily integrate different types of sensors on the bottom and multiple software systems at the top. An open architecture is critical in an Industry 4.0 environment because the IIoT requires the integration of multiple, disparate systems to be effective. The flexibility of its sensors and controls, highly efficient LED offerings, and open software architecture have made Current one of the drivers of the intelligent industrial movement.
Exhibit 3: Current Digital Engine for Intelligent Environments
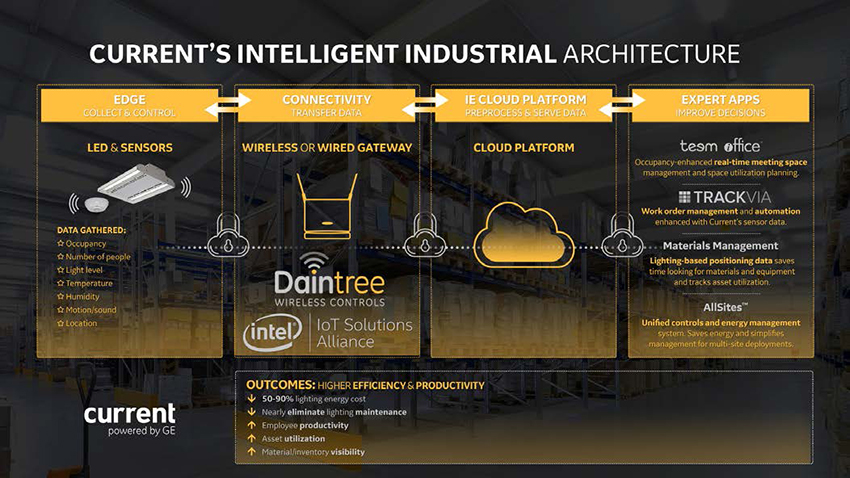
When making the transition to an intelligent environment, lighting is a great place to start. It is a low-risk investment with proven results that can be the catalyst needed to create momentum toward a smarter, more energy-efficient factory. Proper LED deployment quickly pays for itself, with an average of 50% reduction in lighting energy consumption. The quick payback is one reason why the adoption rate of LED in industrial spaces is projected to increase rapidly over the next several years. At a meager adoption rate of 3% in 2014, industrial LED is projected to increase to 76% by 2020 and 80% by 2035.
“Lighting has a great advantage that is very easy to be understood and implemented. We change lights at home, so people are used to the technology,” Marczewski said. “The key factor is its feasibility. With a well-defined scope, the project will ensure that the company will realize the energy savings.”
The US DOE estimates LED can produce a savings of 190 terawatt hours of electricity a year, which equates to the output of 24 large power plants—or the financial equivalent of $15 billion.
Exhibit 4: Current LED to IOT Roadmap, US, 2018
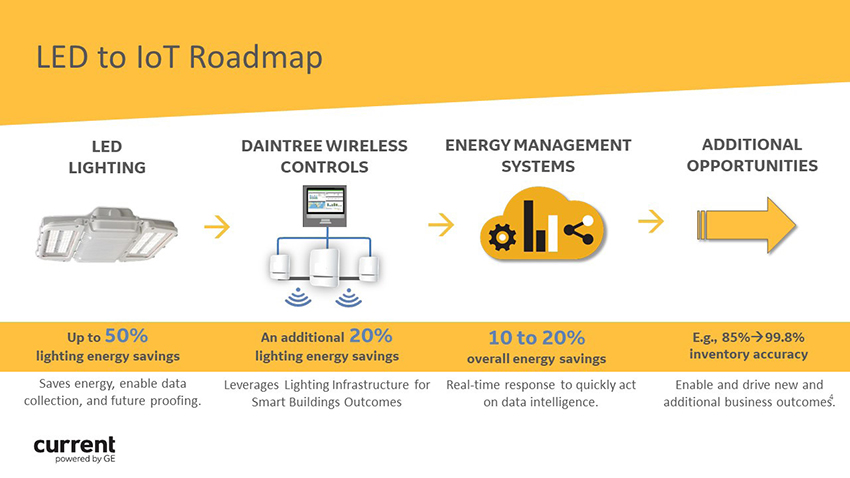
Once the foundation has been set with LED lighting, additional savings and productivity gains can be found by implementing sensors and controls. These devices, such as Current’s Daintree Wireless Control system, can produce up to 20% more savings on top of the 50% from LED lighting alone. The Daintree Wireless Control System provides the ability to implement basic motion or occupancy sensing, but you can also perform more advanced task-tuning, light-level adjustments, and schedule-based control strategies. The same network can be leveraged for more efficient use and predictive maintenance of many other expensive assets such as HVAC systems, RTUs, exhaust fans, forklift charging stations, air compressors, and more. Finally, rather than locking customers into proprietary systems, Daintree is an “open-at-the-bottom” platform, which means it is compatible with an ecosystem of certified third-party ZigBee devices. The ability to integrate with other control vendors provides more flexibility, choice, speed, and lower project costs than in a proprietary system.
Beyond lighting and standard controls, the more sophisticated intelligent environments will feature advanced software applications that drive additional business productivity gains. With Current’s commitment to open architecture, the possibilities are endless. The “open-at-the-top” nature of this system provides clients with an open API that facilitates integration with other solutions. Users are free to construct their own apps or utilize third-party apps to address their unique productivity or energy management needs. Daintree’s network of over 125 technology partners provides enterprises with the ability to select the right technology to remedy highly specific pain points. For example, its partnership with TrackVia can further streamline operations and protect high-dollar assets with mobile-enabled work order management. This freedom to integrate with other systems allows for a truly connected environment, which is the cornerstone of an intelligent factory.
Adding an energy management system to smart LED fixtures allows for real-time responses and quick action when presented with data intelligence, further saving 10-20% in overall energy expenditure. Other efficiency and productivity applications drive new and additional business outcomes; for instance, raising inventory accuracy to 99.8%.
As more capabilities of smart factories are explored, Current’s ecosystem of efficiency and productivity applications continues to grow. Daintree provides clients with an energy management system that not only delivers immediate cost savings but also creates an infrastructure that is future-proof because it can integrate with new advancements as they become available. Generating and analyzing data in real time is possible with visualization tools, such as Current’s AllSites platform, providing critical visibility into portfolio performance and allowing for more informed strategic decisions.
Energy management lays the foundation for system-wide workplace improvement and maximum production capacity. Turning existing equipment, such as light fixtures, into smart objects and connecting those objects to software applications will provide unparalleled and unlimited possibilities. Organizations that equip facilities with the proper infrastructure now position themselves for immediate and future success.